
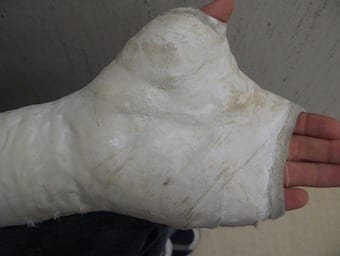
- RECIPE FOR HIGH HEAT CASTING PLASTER FIR GLASS FULL
- RECIPE FOR HIGH HEAT CASTING PLASTER FIR GLASS FREE
I got some important information about refractory castable from your informative blog. Nice tips about Homemade Castable Refractories. Here’s a page from Dan’s Workshop showing John’s refractory mixture in use in the construction of a small electric furnace. It is MUCH easier to work with if you add about 2 cups of water per gallon of cement. The Furnace Cement has about the consistency of roofing tar and is very sticky. You will also want to have some Furnace Cement to use as a sealing coat on your lining.

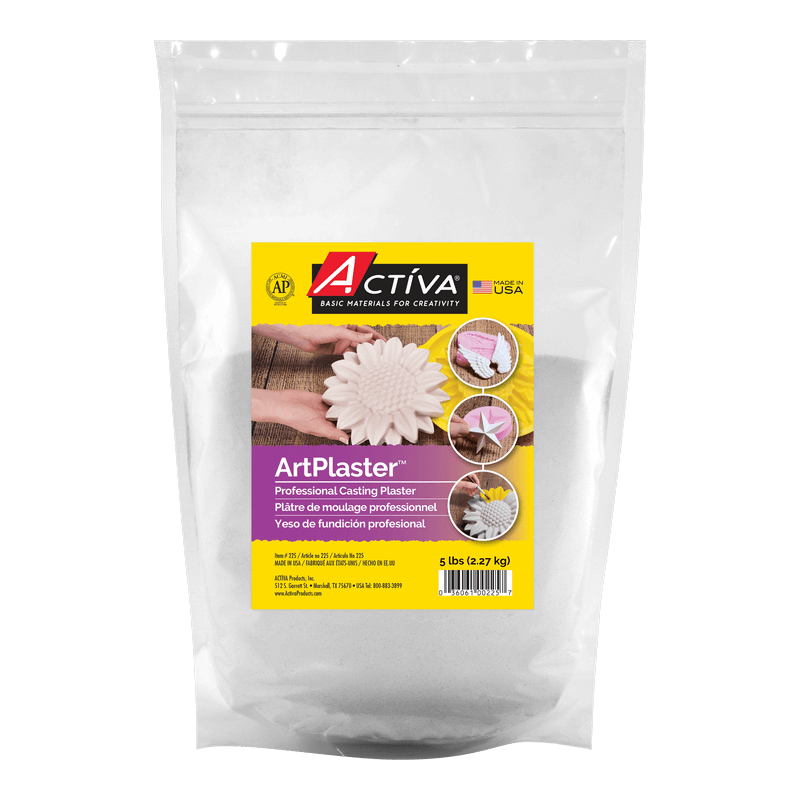
If you use much more than five volumes of Perlite for each volume of Furnace Cement the resulting material will be quite weak. If you use much less than four volumes of Perlite for each volume of Furnace Cement all of the passages between Perlite beads will be sealed and it will take a long time for the cement to set (it needs contact with air). You will need about 1 part (by volume) of Furnace Cement for each 4 parts (by volume) of Perlite so for a two gallon bag of Perlite you will need a half gallon of Furnace Cement. If you can get your hands on ready-made furnace cement, preferably of the “black” 3000 ☏ variety used to make repairs on wood-burning stoves, a simpler recipe is provided by John A. The dry ingredients are then moistened to the texture of “stiff cookie dough,” packed into a form, and allowed to dry thoroughly before bake-out. By volume, it is 3:3:4 Portland cement:perlite:silica sand, mixed together thoroughly, then combined with 4 parts fireclay. Lionel has been experimenting with and writing about home foundry work online for more than a decade, now, and his recipe uses no hard-to-find materials. There are several recipes for “homemade” refractories floating around the web, but Lionel Oliver’s tutorial over on is one of my favorite resources on the subject.
RECIPE FOR HIGH HEAT CASTING PLASTER FIR GLASS FULL
If using a DIY formula, use a gradual “bake out” process in which the cast material is brought up to final operating temperature very gradually, in a series of slow, prolonged stages, with full cooling phases in between. If using a commercial mixture, follow the manufacturer’s directions closely. When working with castable refractory, be mindful of the hazard of heating trapped water too rapidly and causing a steam explosion. Wikipedia quotes ASTM C71 on the definition of refractory: “non-metallic materials having those chemical and physical properties that make them applicable for structures, or as components of systems, that are exposed to environments above 1,000 ☏.” They are commonly used, for instance, to line kilns and other high-temperature furnaces.Ĭastable refractories can be mixed with water, formed, and solidified like cement, but the process of drying the solid before full-temperature use is critical. The cast lid is reinforced with a grid of steel wires to increase tensile strength. Gift the gift of Make: Magazine this holiday season!ĭIY refractory mixture made from Perlite and furnace cement, courtesy of Dan's Workshop. Subscribe to the premier DIY magazine todayĬommunity access, print, and digital Magazine, and more Share a cool tool or product with the community.įind a special something for the makers in your life. Skill builder, project tutorials, and more Get hands-on with kits, books, and more from the Maker Shed Initiatives for the next generation of makers. Membership connects and supports the people and projects that shape our future and supports the learning.
RECIPE FOR HIGH HEAT CASTING PLASTER FIR GLASS FREE
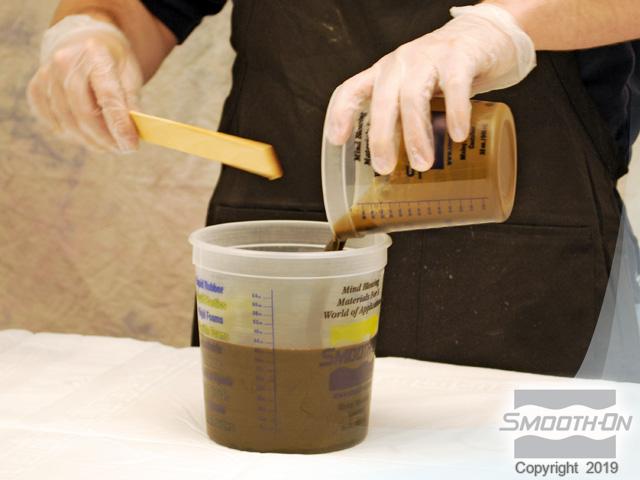
The premier publication of maker projects, skill-building tutorials, in-depth reviews, and inspirational stories,.
